skd11崩刃skd11比熱容,熱加工模具鋼SKD11失效的影響因素
SKD11熱加工模具鋼的失效是一個復雜的技術(shù)問題,可以從材料、設(shè)計、制造和使用四個方面進行分析。
1. 熱加工模具鋼SKD11的化學成分和冶金質(zhì)量
skd11崩刃skd11比熱容,熱加工模具鋼SKD11失效的影響因素,熱作模具鋼SKD11屬于過共析合金鋼類型。該結(jié)構(gòu)存在非金屬夾雜物、碳化物偏析、中心孔隙、白點等缺陷??篃崞谛阅芎?。SKD11鋼一般按質(zhì)量分為普通SKD11鋼和優(yōu)質(zhì)SKD11鋼。優(yōu)質(zhì)SKD11鋼采用更先進的生產(chǎn)工藝,鋼材純凈,組織均勻,偏析輕微,具有更高的韌性和熱疲勞性能。普通SKD11鋼必須經(jīng)過鍛造才能破碎較大的非金屬夾雜物,消除碳化物偏析,細化碳化物,組織均勻。
2. 模具設(shè)計
模具設(shè)計時,根據(jù)成型零件的材料和幾何尺寸確定模具的外形尺寸,以保證模具的強度。此外,過小的圓角半徑、過寬薄壁截面、過寬薄壁截面、孔槽位置不當?shù)龋既菀自谀>邿崽幚砗褪褂眠^程中造成應(yīng)力集中過大,引發(fā)裂紋。因此,模具設(shè)計時應(yīng)避免尖角,孔槽位置應(yīng)合理布置。
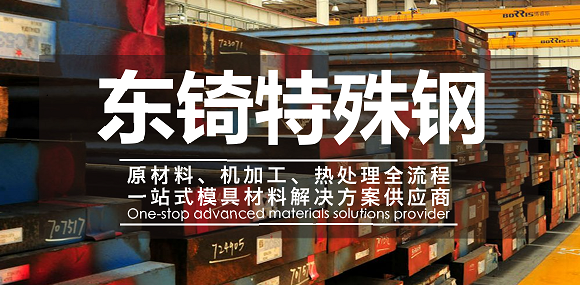
3.生產(chǎn)過程
(1)鍛造工藝
SKD11鋼合金元素較多,鍛造變形抗力大,材料導熱性差。共晶溫度低,不注意就會過熱。因此加熱時應(yīng)預熱至800 ~ 900℃,再加熱至起始鍛造溫度1065 ~ 1175℃。為破碎較大的非金屬夾雜物,消除碳化物偏析,細化碳化物,使組織均勻,在鍛造過程中反復鐓粗和鐓粗,總鍛造比為> 4。因此,SKD11鋼鍛造后應(yīng)緩慢冷卻。
(2)減少
切削過程的表面粗糙度對模具的熱疲勞性能有很大的影響。模具型腔的表面應(yīng)具有較低的粗糙度,不應(yīng)有刀痕、劃痕和毛刺。這些缺陷容易引起應(yīng)力集中和熱疲勞裂紋萌生。skd11崩刃skd11比熱容,熱加工模具鋼SKD11失效的影響因素因此,在模具加工過程中,必須防止復雜零件的角半徑留下刀印,并且必須打磨掉孔、槽邊和根部的毛刺。
(3)研磨
在珩磨過程中,局部摩擦熱很容易造成燒痕、裂紋等缺陷,并在磨削表面產(chǎn)生殘余拉應(yīng)力,導致模具過早失效。磨削熱引起的燃燒會使SKD11模具表面回火,直至形成回火馬氏體。脆性非回火馬氏體層將大大降低模具的熱疲勞性能。如果表面的磨削表面高于800°C和冷卻不足,表面材料將re-austenitized和淬火馬氏體,所以模具將生成一個高的表層結(jié)構(gòu)應(yīng)力、和磨削過程非??焖僦虚g模具表面的溫度上升會導致熱應(yīng)力、組織應(yīng)力的疊加和熱應(yīng)力很容易導致模具磨削裂紋。
(4)電火花
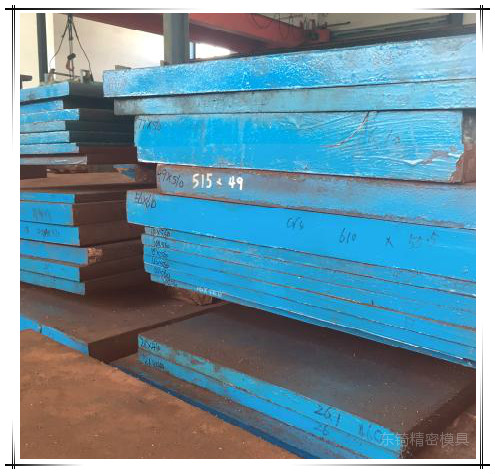
skd11崩刃skd11比熱容,熱加工模具鋼SKD11失效的影響因素,加工是現(xiàn)代模具制造過程中不可缺少的一種精加工方法。火花放電時,局部瞬時溫度超過1000℃,放電處金屬熔化汽化。在電火花加工的表面,有一層薄薄的金屬被熔化和再凝固,并有許多微裂紋。在顯微鏡下,這層薄薄的金屬具有明亮的白色,也就是一層明亮的白色。研究表明,對于高合金化的SKD11鋼,電火花加工形成的表面光亮層組織為原生馬氏體、殘余奧氏體和共晶碳化物,存在大量未回火的原生馬氏體。微裂縫。當SKD11鋼模具在工作過程中受到載荷作用時,這些微裂紋很容易發(fā)展為宏觀裂紋,導致模具早期斷裂和磨損。SKD11鋼模在電火花加工后應(yīng)重新回火以消除內(nèi)應(yīng)力,但回火溫度不應(yīng)超過電火花加工前的更高回火溫度。
東锜精密模具材料有限公司擁有豐富的供應(yīng)經(jīng)驗,為客戶提供從原材料鋸切到粗加工,從熱處理到精加工的一站式整合服務(wù)。
本文部分內(nèi)容來源于網(wǎng)絡(luò),我們僅作為信息分享。本站僅提供信息存儲空間服務(wù),不擁有所有權(quán),不承擔相關(guān)法律責任。如發(fā)現(xiàn)本站有涉嫌抄襲侵權(quán)/違法違規(guī)的內(nèi)容,請發(fā)送郵件至tokaits@163.com舉報,一經(jīng)查實,本站將立刻刪除。